Noise In Warehouse Environments
- Thomas Wood
- Nov 3, 2020
- 6 min read
Updated: Oct 13, 2023
On the face of it, often warehousing environments seem like relatively quiet places to work. We've seen countless workplace noise assessments that are undertaken and focus heavily on factory work but seem to exclude any warehousing or distribution areas "assuming" noise levels are low.

From our experience as Occupational Hygiene professionals, we have undergone exposure monitoring in these environments and have measured noise levels which are high enough to warrant immediate controls to be implemented in order to prevent conditions relating to noise-induced hearing loss. To many, this may come as a surprise, but to us, the risks are just as high in a warehousing environment as they are in a manufacturing or factory environment.
So what causes excessive noise in a warehousing environment?
One of our major clients routinely monitors their warehousing facilities for excessive noise and are currently working with us to design and implement controls in order to reduce noise exposure. We feel that it is important to share our findings to create awareness around the risks associated with noise in a warehousing environment.
Forklift Trucks and Pallet Trucks
Forklift Trucks and Pallet Trucks are often found to generate noise levels in excess of 85dB(A). The surrounding workforce does not necessarily notice the noise, as it becomes very sporadic and intermittent, reducing daily exposures over the course of a shift. However, for the drivers themselves, noise exposures can be very high. These operatives often spend the majority of their shift being exposed to noise, by sitting or walking close to the source. Therefore, are subjected to continuous noise which elevates their daily exposure levels.
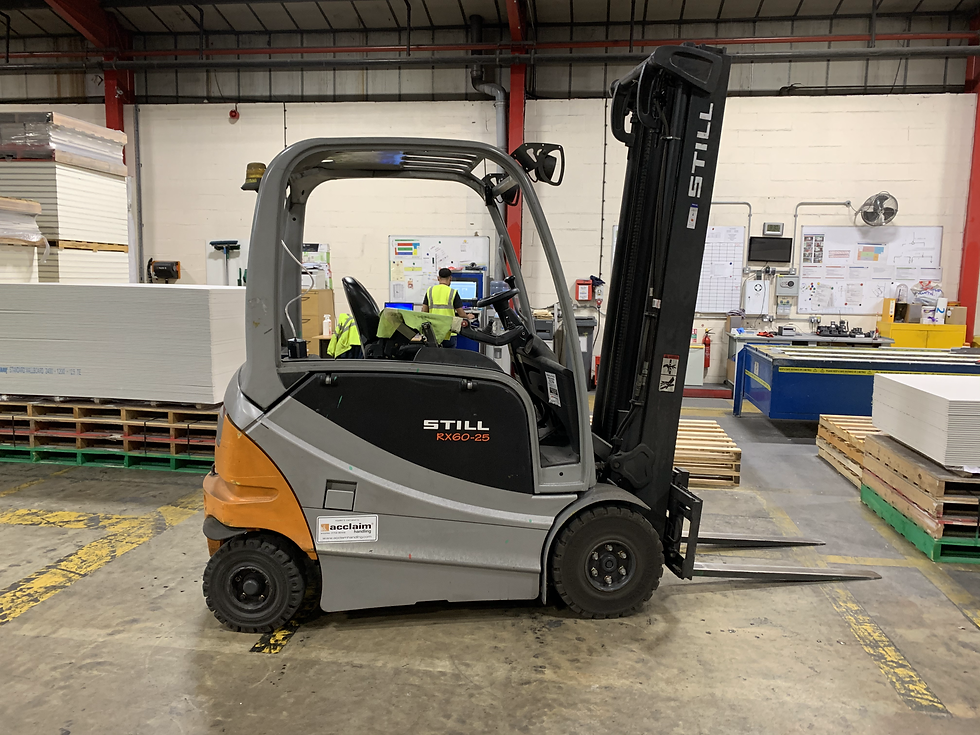
Noise is often emitted by the rattling of the forks. Forklift Trucks and Pallet trucks are often very rigid, the vibration that transfers up through the body of the truck when it manoeuvres over uneven terrain will cause the forks to rattle, which will expose the driver to excessive noise, particularly if the forks are not carrying a load.
An individual who partook in our assessment, who was the driver of a Forklift Truck, was found to have a daily exposure of 87dB(A), equalling the exposure limit value as describes in the Control of Noise at Work Regulations. Workers around him, however, had daily exposures much less. This shows the importance of conducting a thorough risk assessment relating to noise exposure in this type of environment, as these noise levels are deemed high enough to warrant immediate action to be taken to seek a reduction.
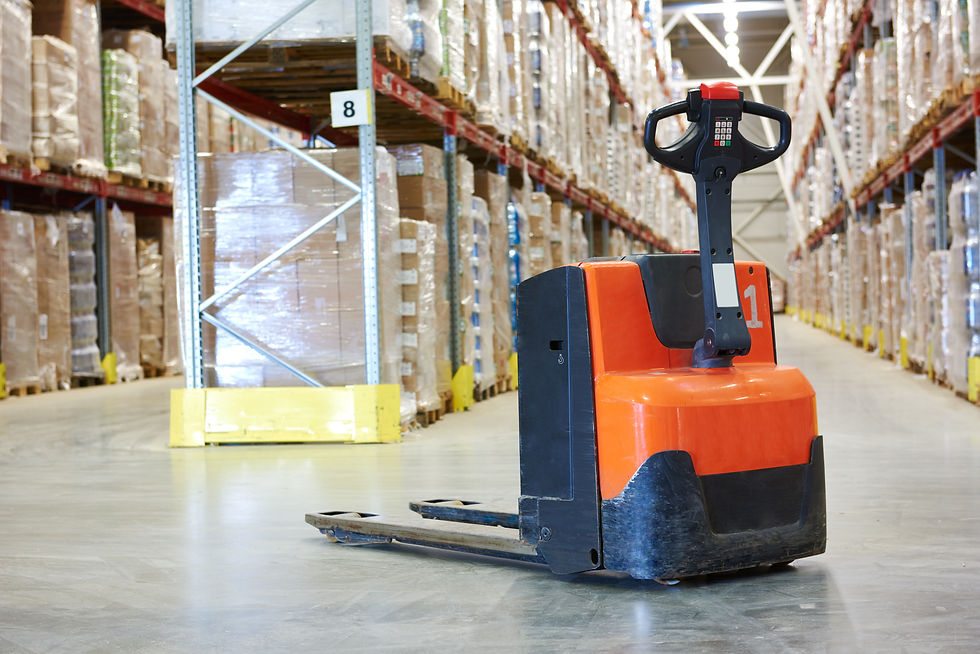
The same can be said for those individuals who move pallets using Pallet Trucks. These are often found to expose workers to high noise levels. Two operatives who were tasked with moving loaded pallets around a warehouse were found to have a daily exposure greater than 85dB(A), the upper exposure action value. In many instances, we see these operatives not wearing hearing protection as it is not deemed necessary. Evidently, further controls are required, perhaps hearing protection being one of the controls provided, especially as a short-term control.
Moving Stock in and out of Trailers
Moving stock in and out of the back of trailers is a high-risk task from a noise exposure perspective. Again, this process often goes uncontrolled resulting in operatives being exposed to excessive noise levels. A measurement obtained from the front of the trailer where the warehouse traffic passes, measured noise levels in excess of 90dB(A) at the source. These levels are excessively high and put the worker at an increased risk of suffering permanent hearing damage as a result.

An example of how noise levels are often increased can be shown above. The ramps used to allow access to the rear of the trailers are usually found to have an embossed pattern pressed into them to help surface grip. As the wheels of the forklift truck or pallet truck move over the surface at speed, excessive noise is generated.
One way of reducing the noise generated by this is to reduce travel speeds. Our client implemented this through routine awareness training and found that in doing so, they were able to significantly reduce noise exposures.
Ensuring that the ramps are secure can also help reduce excessive vibration, usually caused by the metal on metal impacts between the ramp and the base surface. Installing rubber mounts may also help reduce impacts between two hard surfaces, resulting in a reduction in impact noise.
Our client is currently looking at installing rubber surface mats to help reduce noise further as the wheels pass over the embossed surfaces.

A further element to consider is the noise generated inside the trailer of the tractor units. These trailers are enclosed, and they're often not lined with any material that would help suppress noise emitted by the Pallet Trucks or Forklift Trucks moving over the floor surfaces to place the load. That said, noise exposure can be significantly increased as the worker enters the trailer, due to the enclosed space somewhat containing noise in which the operative would be directly situated within, meaning they would be at a greater risk of exposure to high noise levels.
Tape Application

This is a process which often goes unnoticed as being a higher risk task concerning excessive noise exposure. With that said, we have measured the application of tape to be as high as 85dB(A) in extreme circumstances.
Noise is caused by the glue which provides some resistance as the tape is unravelled through its layers as it is applied to a box. The operative is directly exposed as they apply the tape and unknowingly, over the course of their shift, daily exposures can increase significantly.
Often colder warehousing environments may have a significant impact on these elevated noise levels, particularly as the glue is set much harder on the tape, providing more resistance. Warming up the tape may help reduce the resistance and as a result, reduce noise generated.
That being said, it is quite often the case that such processes are not monitored as part of a detailed noise assessment, so it would be beneficial to consider these types of processes when undertaking a suitable and sufficient risk assessment relating to noise exposure.

Wrapping Machines
Often situated in a warehousing environment, machines that wrap palletised goods before dispatch are often significant noise sources. They often use plastic or cellophane to wrap goods by automatically rotating around the palletised items to form a secure barrier.
The use of these machines has been measured in excess of 87dB(A), the exposure limit value, in some cases. These machines are often used sporadically over the course of a shift, and the noise can often go un-controlled due to their short-duration of use. However, noise levels this high, require attention and often these processes do not gain the attention required as a means of controlling noise in the workplace.

Strapping
Strapping up boxes or palletised goods is a process which is carried out in many warehouse environments. That said, these types of processes can be undertaken manually using a hand-held tool, or by an automated machine. Often the characteristics of the noise can be described as being intermittent and sudden. As the straps are tensioned and then cut, the noise is then emitted into the surrounding area. Again, these types of processes often go unaccounted for in a workplace noise assessment and are often left out of any noise exposure related risk assessment.
Hearing Protection in Warehousing Environments
Hearing protection should be the last line of defence against noise. It sits at the bottom of the Hierarchy of Control and should be at least combined with other control measures and not solely relied upon.
Actively encouraging the use of hearing protection is not the way forward, although inevitably it does have its place. With regards to a warehousing environment, the wearing of hearing protection can pose a significant safety risk, particularly where there are moving vehicles operational in the areas of concern.
For this reason, it is vitally important that suitable and sufficient hearing protection is provided of which does not "over-protect" or "under-protect". This is where it is necessary to obtain detailed noise measurement data so that suitable hearing protection can be determined based on an analysis of the noise frequency data. This data is used to determine a suitable attenuation level and a professional occupational hygienist can recommend suitable protectors.
That said, we would always recommend hearing protection with some form of a built-in communication system to be provided in a warehousing environment. Again, maximising communication between operatives is vital in ensuring the safety of the workforce. Again, other control measures should be enforced to help reduce reliance on hearing protection.
In Summary
To summarise, it is important to understand that there are a number of noise-generating activities often found to be overlooked in warehousing environments, as such, organisations are often failing to mitigate the risks associated with excessive noise. This is why it is vital that frequent assessments of these environments are undertaken so that they can be monitored sufficiently and suitable controls can be implemented based on the qualitative and quantitative data obtained by a competent occupational hygienist.
We hope this article goes some way to providing a brief overview of the hazards often found in warehousing environments, from a noise exposure perspective. If you wish to know more on this subject or need support with your assessments, health surveillance or noise management programs then please feel free to get in touch with us through social media or our website (www.workplacescientifics.com), by email at support@workplacescientifics.com or simply give us a call on 01709 931299.
#Noise #Exposure #occupationalhygiene #safety #supporting #businesssupport #occupationalhealth #occupationalhealthandsafety #healthandsafety #healthandwellbeing #safetyfirst #safety
Commentaires